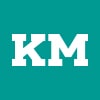
Дирижабль с рамой из углекомпозита грузоподъемностью 60 тонн
рубрика: технологии
Exel Composites и Flying Whales разработают дирижабль грузоподъемностью 60 тонн с несущей конструкцией, состоящей из углекомпозитных труб.
Производитель композитов Exel Composites сотрудничает с французским производителем и оператором дирижаблей Flying Whales для разработки тонкостенных труб из углеродного волокна для современного дирижабля. Дирижабль будет доставлять до шестидесяти тонн груза в отдаленные и труднодоступные места по всему миру. Это также позволит сократить выбросы по сравнению с наземным и воздушным транспортом. Производитель композитов будет оказывать научно-исследовательскую поддержку на этапе прототипирования жесткой конструкции дирижабля, разрабатывая и производя около 80 км труб из углеродного волокна, необходимых для воплощения этой концепции в реальность.
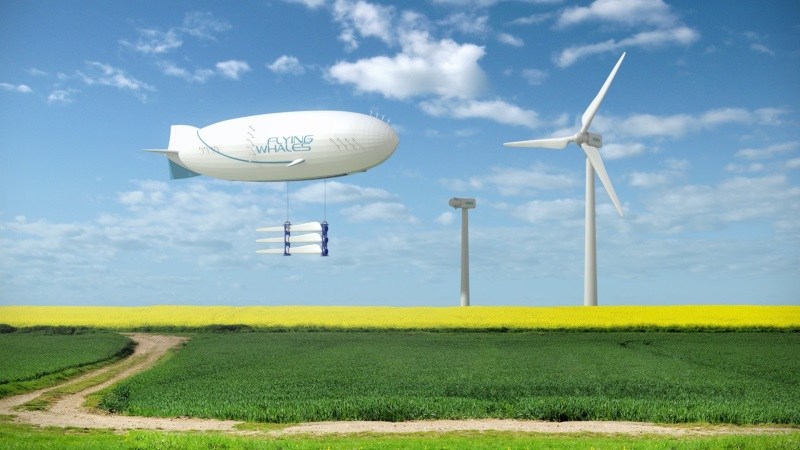
Дирижабль Flying Whales с трубами из углеродного волокна (фото: Flying Whales)
Flying Whales является разработчиком LCA60T, дирижабля вертикального взлета и посадки (VTOL) длиной 200 м. Дирижабль будет функционировать как бортовой кран, перевозя груз и транспортируя его заказчику, снижая зависимость от воздушного и наземного транспорта и устраняя узкие места в морских портах. Дирижабль может быть использован для транспортировки деревьев при транспортировке пиломатериалов, лопастей ветряных турбин на коммунальные станции и, что самое удивительное, целой портативной больницы, направленной на обеспечение всеобщего здравоохранения в некоторых из самых отдаленных районов мира.
«Поскольку этот дирижабль является одним из самых больших из когда-либо разработанных, рама должна быть в состоянии распределить всю нагрузку конструкции», — объяснил Гийом Кляйн, менеджер по развитию бизнеса Exel Composites. «Мы тесно сотрудничаем с Flying Whales, чтобы разработать уникальную трубу, отвечающую техническим требованиям и спецификациям, необходимым для того, чтобы сделать этот проект жизнеспособным. Большинство аэрокосмических стандартов пока не охватывают дирижабли, вместо этого сосредоточившись на самолетах и вертолетах».
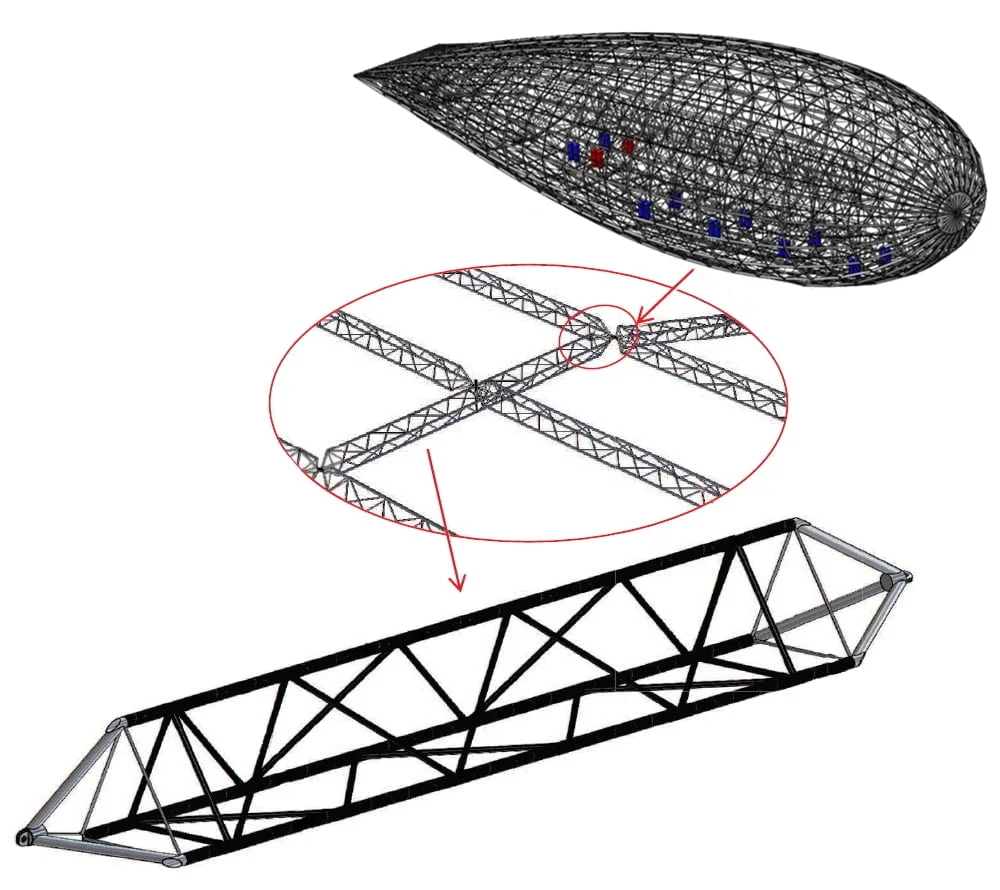
Проектирование и изготовление конструкционных деталей из композиционных материалов для дирижабля
«Нам нужен был как поставщик труб из углеродного волокна, произведенных методом вытягивающей намотки, так и партнер по исследованиям и разработкам, понимающий аэрокосмические стандарты и области применения, чтобы помочь воплотить наше видение в жизнь. Exel предоставила нам и то, и другое», — объяснил Винсент Гибу, генеральный директор Flying Whales.
Финский производитель композитов Exel Composites был выбран из-за огромного опыта в области изготовления конструкционных композитов.
«Для каждого дирижабля требуется 80 км труб из углеродного волокна», — продолжил Кляйн. «Метод вытягивающей намотки идеально подходит для этих применений, поскольку он позволяет получать более прочные изделия, по сравнению с другими методами. Кроме того, будучи непрерывным производственным процессом, он позволяет нам производить большие объемы труб, необходимых для этого проекта, сохраняя при этом качество, стабильность и однородность».
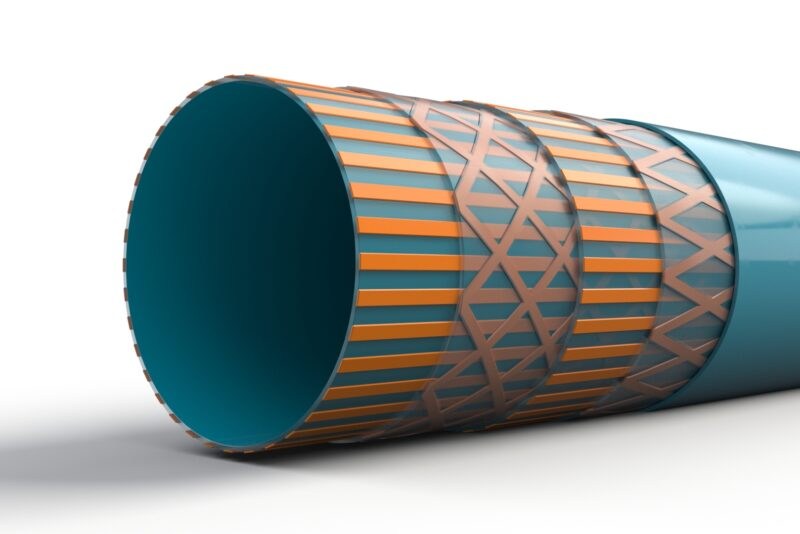
Вытягивающая намотка сочетает в себе два метода: пултрузии и непрерывной намотки нити, в результате чего получается профиль с превосходной прочностью обруча, длительной прочностью и модулем упругости, с гладкой поверхностью.
В дополнение к однонаправленному выравниванию волокон, в процессе вытягивания используется винтовая намотка армирующих волокон, что дает возможность направлять как однонаправленные волокна, так и винтовые намотки (от нескольких градусов до 90 градусов). Такое сочетание направлений волокон обеспечивает композитные преимущества, такие как более тонкие стенки или соответствие определенным требованиям к прочности или жесткости.
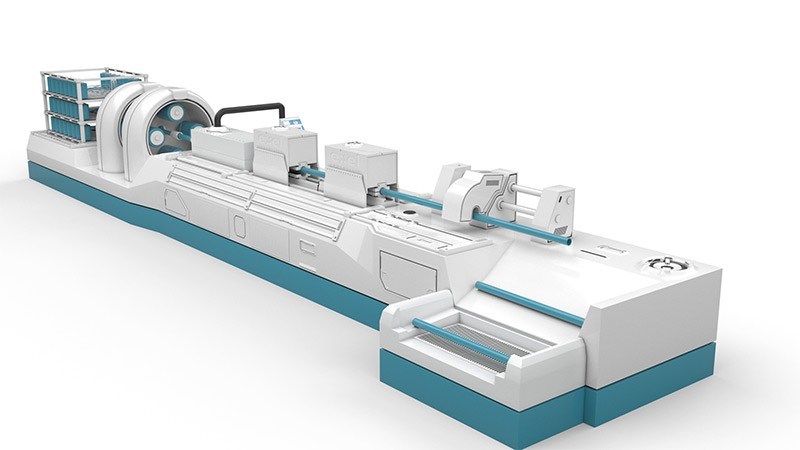
Производственный процесс с вытягиванием является непрерывным процессом, в результате которого получается стабильный выход композитного профиля, который в конце процесса разрезается по длине. Это называется pull-winding, потому что производимый профиль сначала «наматывается» по спирали на армирующие волокна (в дополнение к однонаправленным волокнам), а затем протягивается в процессе.
Процесс вытягивания и намотки состоит из четырех основных технологических этапов; выравнивание арматуры и пропитка, формовка и нагрев смолы в матрице; процесс вытягивания и, наконец, резка ножницами в воздухе.